Adrian here, with an update on the happens at MCQN Ltd over the past fortnight.
As a tiny company one of the continual challenges is balancing the amount of work to do with the available capacity to do it. The start and end of projects tend not to neatly line up; and even when you think they will then an unexpected bug can still throw your planning out as it's an art as much as it is a science.
The product side of the business—particularly developing new products where there isn't any fixed timescale—helps to smooth that out a little. Filling in any gaps with useful work, and allowing people to be drafted in to help with client work at the cost of a delay to the product work.
The Ackers Bell has definitely suffered from that in the past. At the moment that's not the case. Right now the sticking point is finding CNC services who will give us a quote for making the frames; not helped by the supply chain issues around plywood caused by the Russian invasion. Ross is chipping away at this, and slowly making progress.
Things have been especially congested over the past two weeks. A combination of lots of different things: wrapping up one client project; quoting for a new one; sending out My Baby's Got LED orders; making up some new boards to re-stock the shop after the orders exhausted the existing stock; helping a couple of Museum in a Box customers with some support niggles as they ready boxes for new projects; and more.
Another project I've been closing out is the Metroscopes work for FACT. The code was all written a while back, and we just needed to find a suitable time to check the operation of the Ethernet-to-RS422 bridge which will let the code talk to the Metroscope lampposts. It all went smoothly. So this week had some devops to schedule the code to get new search results to run periodically; and another system service to automatically start (and monitor) the code to send the results to be displayed.
Alongside all that, I've had some more strategic thinking to do. Tbat also involved chatting to the accountant, plus some company structure research. Not the best timing, but there should—fingers crossed—be some exciting news to share if/when it gets worked out.
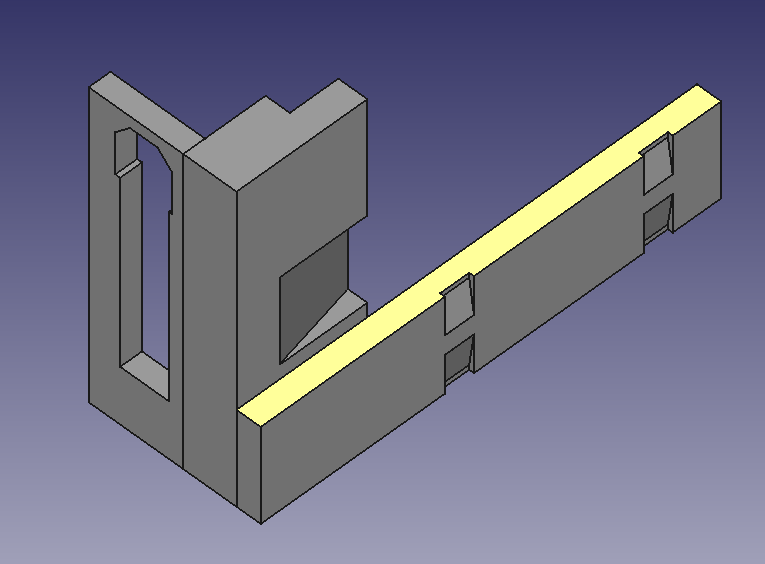
Chris has been back in FreeCad making a part for Museum in a box. It's an add-on for travelling boxes to hold their Raspberry Pi more securely. Some of our customers have been sending boxes out on tour, to take the collections to the people rather than the other way round. Spending so much time in the post means the boxes suffer more vibration than we'd anticipated. This, we hope, will beef up the connections. Tha's shown an unexpected benefit of working with folk who are 3D printing objects in their museum projects. We can email them a design for a new part, and they can print it out to upgrade their box themselves! It's particularly handy when they're over in the US.
On the My Bike's Got LED front, Chris is working on some data logging. He's setting up an INA219 i2c Current module to gather some data from the battery charging circuits. This will give us a more detail of the charging profile and help us optimise the circuit. And we can use it for some more objective testing of the circuit in its windmill charging form.