Let's get back on the #weeknotes wagon, with a set that are more monthnotes. There's been lots going on, but I've been pretty quiet in sharing any of it. There's also been little activity on the sales and marketing side of My Baby's Got LED and so the main people-interested-in-controllable-LED-displays season is passing by without me having the bandwidth to properly offer our solution.
I think that's a good reminder that I need to get back to hiring someone to help with that side of the business. Something I've been continually aware of, but short-term workload has meant it's been sidelined. As ever, the short-term hasn't been quite as short as I'd anticipated, but has eased enough now for the staffing to get back to a priority. That's one of this week's tasks.
So, what have I been up to? Three things, mostly. The start of this five-week period was all about pen plotters, and it ended all about new product development. As we worked through the weeks the proportions steadily shifted, so most of it had some level of both projects vying for my time.
Pen Plotting
Snoof was back in to help out some more with the assembly.
Getting the three additional pen plotters finished was reasonably uneventful. Lots of careful building, pulling together the various bits and pieces, and (it seemed) plenty of measuring and selecting a variety of bolt sizes.
We documented the process as we went, resulting in a 1400-word instruction manual, plus an assortment of CAD files. That's all held in the client's github repository for the project, alongside the code for the app.
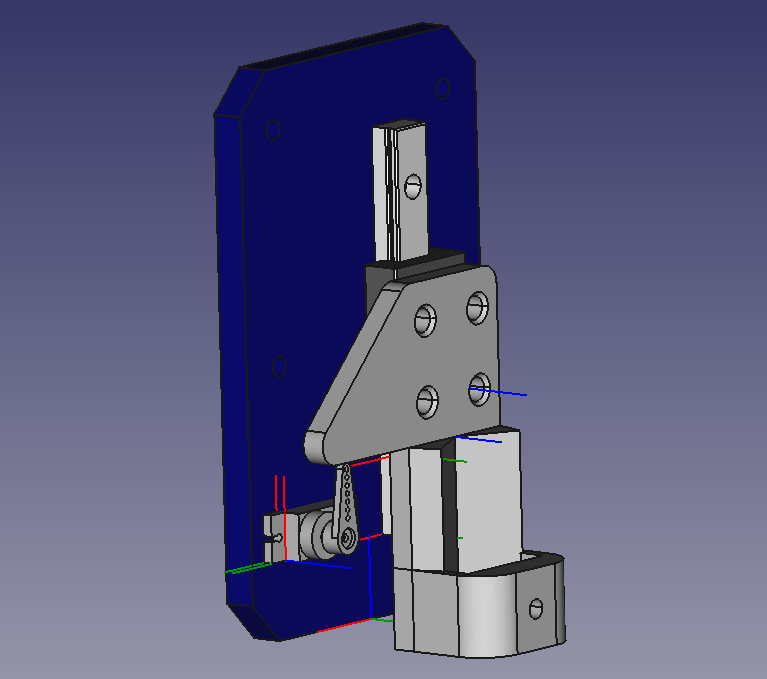
It was very satisfying to see the pen holder go from the initial CAD design (above) to a finished and working mechanism:
With the plotters built, I actually ended up with my furthest trip since 2019, as I paid a visit down to London for some final tweaks and checking over the installation on site.
London wasn't too different from what I remember of it pre-pandemic, but there were noticeably more bikes around—especially cargo bikes! Good to see.
My Bike's Got LED
Talking of bikes...
I finished off laying out the PCB for the batter-operated spin on our My Baby's Got LED board, and ordered a batch of prototypes.
When they arrived I got a couple soldered up to test and found that they refused to power up.
After some debugging I found that the protection chip for the battery wasn't enabling the over-charging side of the circuit (despite the battery being within the safe range). Checking the datasheet again, this section stood out:
Note: When a battery is connected to FS312F-G for the first time, it may not enter the normal condition (dischargeable may not be enabled). In this case, short the CS and VSS pins or connect to a charger to restore to the normal condition.
That "may not" seems to be "always" in my experience. Still, that pointed to a fix and shorting the relevant pin to ground did result in the system coming up fine, and everything seemed to be working fine!
I'll fix the design for the next batch of boards, but needed a workaround for this batch. After some time at the electronics workbench with the soldering iron and some enamelled wire, I had a bodge wire fixing the bug on each of the current boards.

That gave us enough boards for some tests. I've got one set up on my bike, with 1.5m of LEDs lining the triangle in the frame, and Jackie Pease has been working on some wearable modules for local bike co-operative Peloton Liverpool to use in their group rides over the winter.
They're using two 93 LED discs—one on your front and one on the back—under a vacuum-formed diffuser. I'll share some photos and video in future, but you can see one of the first units in this clip from our Bonfire Night ride:
It's good to have the prototypes getting proper use, so I can see what they're like to live with.
One thing that's already shown up is the heat dissipation of one part of the circuit. As you add more and more lights, you need more current to drive them all. The part of the circuit that boosts the battery voltage up to the 5V needed by the LEDs is worked harder as the current increases, and when running it at two amps it gets pretty toasty. It will happily run with that level of demand, but makes one part of the board too hot to touch.
The components are all rated to well above two amps, but then they're also staying well within their temperature limits too—even if that's above the comfortable limits for a human finger! So I need to improve that part of the design. In the meantime we can run the lights with a current limit in the WLED software; that will have the bonus side-effect of making the batteries last longer...
Teleprinter Restoration
Alongside the plotting and lights, we've continued plugging away at the World War II teleprinter.
There have been two more episodes in our video diary, as we skipped one session as I was at a march for COP26 and Paul and Mike were in different countries on holiday.
We seem to have hit a frustrating stage in development, where things should be almost finished but there's an annoying bug that makes the operation worse that it had been. I'm sure we'll work our way through it, but it's definitely got us stumped at the moment.